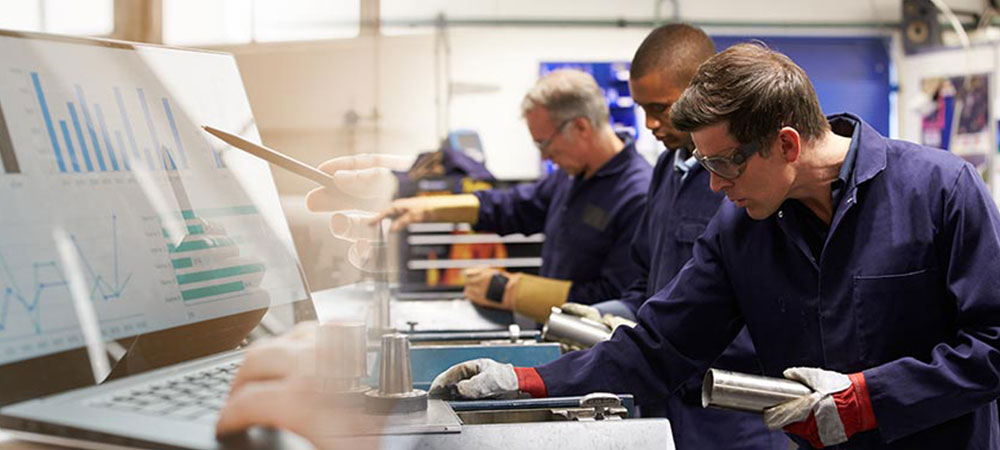
An informative system to manage continuous improvement
The continuous improvement activity within a company is normally split our into focused improvement and systematic improvement. Today, people refer to the former through the term Kai-zen and to the latter with a series of abbreviations related to the various methodologies (World Class, Six Sigma, etc.) which find a synthesis in the expression “Excellence system”.
The Kaizen approach, widespread thanks to the Toyota Production System or TPS, has always been linked to a papery management of the various phases of this activity, as per Japanese tradition. Every Kaizen project, in fact, is usually managed through a board on which are posted the documents that the kaizen team processes in the meetings for the implementation of the various activities. The forms of the tools, such as 5w + 1h, 4M Ishikawa, 5 whys, control cards, etc., take subsequently place on the board.
As long as this approach concerns only one production site, the classical methodology is sufficient to allow “on sight” control of what is done by the different teams. The introduction, the consolidation and the extension of this approach within a large company having different production sites, however, requires the support of an information system for the remote management of the activity and for the identification and dissemination of best practices.
His first application for large-scale kaizen management was created by Exagogica in 2014 within the online PD application for FCA. The application workflow basically allowed to manage the so-called “quick kaizen” that in the WCM methodology doesn’t need to define a team and could be carried out independently by a single worker.
In FCA, Maserati and Marelli the first applications to manage the improvement of process
The application, initially developed within the Maserati factory in Grugliasco, had a significant success, spreading among the Italian plants of the FIAT group and managing more than 200,000 improvement proposals and 7,000 kaizen. Of particular relevance in the application were the reporting of the levels of proactivity and the savings generated by each worker and a reporting system that allowed to manage the recognition and rewarding plans associated with the development of the involvement of the operators. The system also allowed to manage the catalog of all the improvements made, offering tools to carry out searches by component, type of process, characteristics of the problem and of the solution implemented.
After the customized system for FCA, Exagogica developed the “Compass Room” continuous improvement management system for Magneti Marelli. In this system, created to unify the management of the Cost Deployment, Focused Improvement and People Development pillars, we implemented the main tools required for a large scale kaizen management.
In particular, the system we created offered the management of the knowledge inventory for the selection of the best team leaders and team members, the forecast of the workload to avoid work overloads, the planning of on-the-job training through the skill matrix, the use of data on savings in staff classification projects and the identification of exceptional people.
Thanks to the experience developed on these large customized projects, we were able to gradually introduce the logic and the tools of the Deming cycle into our standard software modules. In particular, in 2017 we released the first version of the Panoptikon 2.3 EHS Management module with the digitalization of the 4 phases of the Deming cycle (Plan, Do, Check, Act) and all the connected tools. The module, already used in Elica S.p.A., was then updated in 2019 and adopted by Denso on 18 plants of the Tec business line.
It is born Kaizen management solution
Also in 2019, we completed the first version of the 2.5 Kaizen management module, which finally offered an integrated and complete system for lean manufacturing activities management, focused on the Kaizen methodology.
This module, at the basis of our current offer for Blue room and Compass room management, delivers the collection of proposals for focused improvement, the management of the feasibility analysis, the choice of the team leader and team members, the schedule of the project. For the implementation phase, the system delivers the management of costs and savings forecasts, the reporting of the activities and the uploading of the related documents. The check phase of the economic impact of the project is assisted by tools that facilitate standard costs control and monthly reporting. At the end of the process, the system delivers the archiving of the project, its dissemination as best practice and also the planning of its diffusion within the organization on similar processes.
Alessandro Obino, CEO Exagogica
© Riproduzione riservata